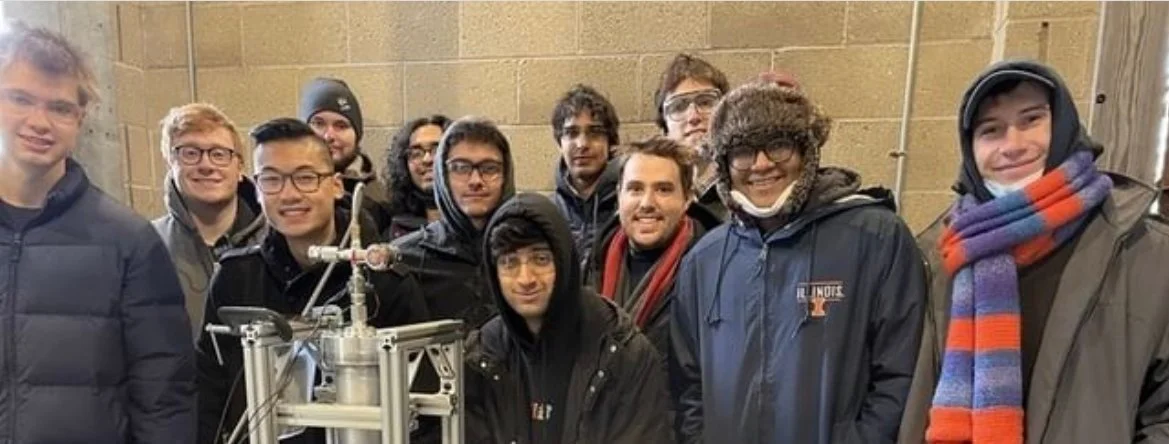
Hybrid Engine Testing
Hydrostatic Testing
During hydrostatic testing, components of the rocket are tested for strength and leaks. For the hybrid rocket engine, the combustion chamber, oxidizer tank, and feed system were all pressure tested to verify structural integrity. We were able to successfully pressurize the combustion chamber to 45 bar and the oxidizer tank to 69 bar.
Cold Flow Testing
After successful hydrostatic tests, we then moved forward with cold flow testing. Since this test is also our first opportunity to observe pressurized oxidizer flow through the feed system, cold flow also serves as a validation for the structural integrity of the tubing while experiencing operational conditions. The four main objectives of a cold flow test are to confirm the expected mass flow rate, characterize the discharge coefficient, monitor the jitter of components, and withstand pressurized flow up to 45 bar.
Before using pressurized oxider, we first decided to conduct a cold flow lite. For the lite test, we substituted the oxidizer with water. After three successful cold flow lites, we are preparing for a full-scale cold flow with the pressurized oxidizer.
Hot Fire Testing
After we complete a successful full-scale cold flow, the engine testing team will be preparing for a hot fire test! Hot firing of the engine provides the opportunity to verify that the engine fires without any significant issues, and allows us to characterize the thrust generated. The test will primarily determine that the engine is capable of providing the expected thrust for the total expected burn time. The test will be deemed as successful if we observe a burn time within a half a second of the expected 4.5 second burn time, and a peak thrust value within a 50% margin of error of the theoretical value of 4kN.